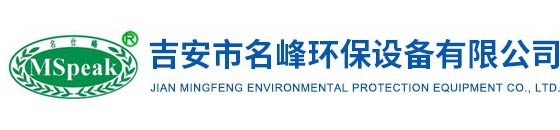
- 加入收藏
- 您可以撥打: +86 379 64122001
高速角接觸球軸承的應用
后退數(shù)控金切機床的高速主軸系統(tǒng),顧名思義是具有高回轉(zhuǎn)速度,但這并無嚴格的界限。對作為高速切削機床代表的加工中心和數(shù)控銑床而言,一般是指最高轉(zhuǎn)速≥10,000r/min的主軸系統(tǒng),并相應具有高的角加(減)速度,以實現(xiàn)主軸的瞬時升降速與起停。為適應制造業(yè)對機床加工精度愈來愈高的要求,高速切削主軸還應有較高的回轉(zhuǎn)精度,通常要求主軸的徑向跳動小于1或2μm,軸向竄動小于1μm。此外,主軸也要有足夠的靜、動剛度,以承受一定的切削負荷和保持高的回轉(zhuǎn)精度。
傳統(tǒng)的主軸系統(tǒng)包含皮帶、齒輪等中間傳動環(huán)節(jié),不僅轉(zhuǎn)動慣量大,難于實現(xiàn)高的角加(減)速度,而且高速時也難于解決中間傳動環(huán)節(jié)出現(xiàn)的振動和噪聲。因此,現(xiàn)在的高速主軸系統(tǒng)大多是把電動機與主軸“合二而一”、將傳動鏈縮短為零的電主軸單元,結(jié)構上基本是把主電動機置于主軸前后軸承之間。這樣的電主軸,軸向尺寸較短,結(jié)構緊湊,主軸剛度高,出力較大。德國GMN公司用于加工中心和數(shù)控銑床的電主軸就是這種結(jié)構,其軸承是適合高速運轉(zhuǎn)的精密角接觸球軸承(一般相當于國際標準P2和P4級),所有關鍵零件都必須進行精密加工和精密裝配,同時還要用恒溫冷卻水(GMN為23±0.7℃甚至±0.3℃)對主電機的定子和前后軸承進行冷卻。GMN用于加工中心和數(shù)控銑床的電主軸共有20幾種型號,最高轉(zhuǎn)速從8000r/min到60000r/min,功率從5.5kW到76kW,扭矩從0.9Nm到306Nm。
現(xiàn)在,也有極少數(shù)高速輕切削銑床,使用將主電機置于主軸后軸承之后的電主軸。這種結(jié)構的電主軸軸向尺寸長,但可改進散熱條件。此外,某些主軸最高轉(zhuǎn)速在10000r/min至15000r/min的加工中心和銑床,不是采用電主軸而是通過薄膜式之類的聯(lián)軸節(jié),將主電動機與主軸直接連接,從而省去主軸冷卻系統(tǒng)。不過,此方式既增加了轉(zhuǎn)動慣量,影響角加(減)速度,而且兩者直連后的非直線性又會引起振動(轉(zhuǎn)速愈高對直線性的調(diào)準要求也愈高),故不宜用于主軸轉(zhuǎn)速更高的機床。
當前的高速電主軸,幾乎都是內(nèi)置異步交流感應電動機。異步型電主軸的優(yōu)點是結(jié)構較簡單,制造工藝相對成熟和安裝方便,特別是可以更大限度地減弱磁場,易于實現(xiàn)高速化。此種主軸電機也正在進一步改進,比如日本三菱電機公司最近開發(fā)出可減少電損耗和縮短定子長度的高速、高效率內(nèi)置感應主軸電動機。
最近,國外正研討在電主軸中內(nèi)置交流永磁同步電動機的問題。與異步感應電動機相比,永磁同步電動機有如下優(yōu)點:用永磁材料制造的轉(zhuǎn)子在工作過程中不發(fā)熱,解決了目前內(nèi)置的異步感應電動機轉(zhuǎn)子發(fā)熱且難于充分冷卻的問題;功率密度大,工作效率高,即可用較小的尺寸得到較大的功率和扭矩;低速性能好,易于實現(xiàn)精密控制等。然而,永磁同步電動機也有其弱點,那就是功率容量有限,弱磁困難,不利于實現(xiàn)高速化。故迄今為止,只有個別機床公司有內(nèi)置永磁同步電動機的電主軸在展會上亮相,而專業(yè)化的電主軸制造廠尚沒有此種產(chǎn)品出售。有不少人認為,對在弱磁場運行的高轉(zhuǎn)速電主軸,似乎用異步感應電動機驅(qū)動更為合適。
目前主要采用PWM變頻調(diào)速技術來實現(xiàn)電主軸的高速化,執(zhí)行此項任務的既有普通變頻調(diào)速器,又有矢量控制驅(qū)動器。前者為恒轉(zhuǎn)矩驅(qū)動,輸出功率與轉(zhuǎn)速成正比;后者在低速端(額定轉(zhuǎn)速以下)為恒轉(zhuǎn)矩驅(qū)動,在中、高速端為恒功率驅(qū)動。高速加工中心和數(shù)控銑床之電主軸,基本上都采用后者(即矢量控制驅(qū)動器)。矢量控制驅(qū)動器又有開環(huán)型和閉環(huán)型之分,閉環(huán)型在主軸上裝有高性能編碼器作為檢測元件,以實現(xiàn)位置和速度反饋,從而有更好的動態(tài)性能,還可以實現(xiàn)主軸的定向準停和C軸功能。
高速主軸用的軸承
數(shù)控金切機床高速主軸的性能,在相當程度上取決于主軸軸承及其潤滑。滾動軸承由于剛度好、精度可以制造得較高、承載能力強和結(jié)構相對簡單,不僅是一般切削機床主軸的首選,也受到高速切削機床的青睞。從高速性的角度看,滾動軸承中角接觸球軸承最好,圓柱滾子軸承次之,圓錐滾子軸承最差。
角接觸球軸承的球(即滾珠)既公轉(zhuǎn)又自轉(zhuǎn),會產(chǎn)生離心力Fc和陀螺力矩Mg。隨著主軸轉(zhuǎn)速的增加,離心力Fc和陀螺力矩Mg也會急劇加大,使軸承產(chǎn)生很大的接觸應力,從而導致軸承摩擦加劇、溫升增高、精度下降和壽命縮短。因此,要提高這種軸承的高速性能,就應想方設法抑制其Fc和Mg的增加。從角接觸球軸承Fc和Mg的計算公式得知,減少球材料的密度、球的直徑和球的接觸角都有利于減少Fc和Mg,所以現(xiàn)在高速主軸多使用接觸角為15°或20°的小球徑軸承??墒?,球徑不能減小過多,基本上只能是標準系列球徑的70%,以免削弱軸承的剛度,更關鍵的還是要在球的材料上尋求改進。
與GCr15軸承鋼相比,氮化矽(Si3N4)陶瓷密度僅為它的41%,用氮化矽制作的球要輕得多,自然在高速回轉(zhuǎn)時所產(chǎn)生的離心力和陀螺力矩也要小得多。與此同時,氮化矽陶瓷的彈性模量和硬度是軸承鋼的1.5倍和2.3倍,而熱膨脹系數(shù)僅為軸承鋼的25%,這既可提高軸承的剛度和壽命,又使軸承的配合間隙在不同溫升條件下變化小,工作可靠,加之陶瓷耐高溫且不與金屬發(fā)生粘咬,顯然用氮化矽陶瓷制作球體更適合進行高速回轉(zhuǎn)。實踐表明,陶瓷球角接觸球軸承與相應的鋼球軸承相比速度能提高25%~35%,不過價格也要高一些。
國外將內(nèi)外圈為鋼、滾動體為陶瓷的軸承統(tǒng)稱為混合軸承。目前混合軸承又有新發(fā)展:一是陶瓷材料已用于制作圓柱滾子軸承的滾子,市場上出現(xiàn)了陶瓷圓柱混合軸承;二是用不銹鋼(比如FAG公司用氮化不銹鋼Crodinur30)代替軸承鋼制作軸承的內(nèi)外圈特別是內(nèi)圈,由于不銹鋼的熱膨脹系數(shù)比軸承鋼小20%,自然在高速回轉(zhuǎn)時,因內(nèi)圈熱膨脹所造成的接觸應力增大趨勢會受到抑制。
眾所周知,dmh值是表達滾動軸承高速性能的速度因子(dm是滾動軸承內(nèi)、外圈的平均直徑,單位mm;h是軸承的轉(zhuǎn)速,單位r/min)。角接觸球軸承的高速性能不僅與球的接觸角、直徑和材料相關,而且與軸承的潤滑方式關系密切。目前滾動軸承有脂潤滑、油霧潤滑和油氣潤滑三種方式,其中油霧潤滑雖然效果不錯,但污染環(huán)境和危害工人健康,國外已很少采用。
脂潤滑是最簡單和環(huán)保性最好的一種潤滑方式。由于脂在超高速運轉(zhuǎn)下容易變質(zhì),故其dmh值較低,軸承為鋼球時僅達80×104,為陶瓷球時可達110×104(FAG公司開發(fā)的新一代低溫軸承其dmh值還可以在此基礎上增加10%左右)?,F(xiàn)在高速主軸軸承用得最多的是油氣潤滑方式,它是定時、定量地供給軸承以油—氣混合物,使軸承各部位獲得最佳的微量潤滑并把污染減至很小。采用油氣潤滑的鋼球或陶瓷球角接觸球軸承,其dmh值一般可分別達到到140×104和210×104,若采用比較特殊的油氣潤滑方式,陶瓷球角接觸球軸承的dmh值可達250×104甚至更高一點為特殊油氣潤滑方式的一種,在試驗室內(nèi)其dmh值已達280×104)。
高速電主軸滾動軸承的配置形式有多種,但比較典型的是前、后軸承呈“O”型布局的兩對角接觸球軸承。由于后軸承也是角接觸球軸承,一般要設置滾珠套以便讓后軸承能沿殼體軸向移動,使得主軸受熱后可自由向后方膨脹。一般說來,角接觸球軸承需要在軸向有預加負荷才能正常工作,預加負荷愈大,軸承的剛度愈高但溫升也愈大。比較簡單的辦法是,根據(jù)電主軸的轉(zhuǎn)速范圍和所要承受的負載,選定一個最佳的固定預加負荷值;更好的辦法則是預加負荷能隨主軸轉(zhuǎn)速改變而調(diào)整,在高轉(zhuǎn)速時減小預加負荷,在低轉(zhuǎn)速時增加預加負荷。
- 聯(lián)系我們
銷售經(jīng)理:王經(jīng)理
移動電話:18939000078銷售熱線
電 話:0379-64122001
0379-64122002技術中心
電 話:0379-64122008
電子郵箱:techsupport@sbi.com.cn
地 址:中國洛陽市西工區(qū)河南洛陽工業(yè)園區(qū)緯四路
傳 真:0379-64122006
電子郵箱:sbi@sbi.com.cn
-