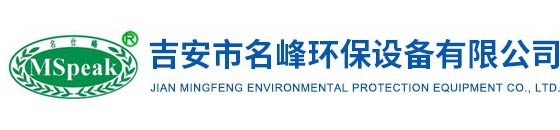
- 加入收藏
- 您可以撥打: +86 379 64122001
淺談粉末冶金原理
后退粉末冶金是制取金屬或用金屬粉末(或金屬粉末與非金屬粉末的混合物)作為原料,經(jīng)過成形和燒結(jié),制造金屬材料、復(fù)合以及各種類型制品的工藝技術(shù)。粉末冶金法與生產(chǎn)陶瓷有相似的地方,因此,一系列粉末冶金新技術(shù)也可用于陶瓷材料的制備。由于粉末冶金技術(shù)的優(yōu)點(diǎn),它已成為解決新材料問題的鑰匙,在新材料的發(fā)展中起著舉足輕重的作用。
1粉末冶金原理的特點(diǎn):
粉末冶金在技術(shù)上和經(jīng)濟(jì)上具有一系列的特點(diǎn)。
從制取材料方面來看,粉末冶金方法能生產(chǎn)具有特殊性能的結(jié)構(gòu)材料、功能材料和復(fù)合材料。(1)粉末冶金方法能生產(chǎn)普通熔煉法無法生產(chǎn)的具有特殊性能的材料:
1) 能控制制品的孔隙度;
2) 能利用金屬和金屬、金屬和非金屬的組合效果,生產(chǎn)各種特殊性能的材料;
3) 能生產(chǎn)各種復(fù)合材料;
(2)粉末冶金方法生產(chǎn)的某些材料,與普通熔煉法相比,性能優(yōu)越:
1)高合金粉末冶金材料的性能比熔鑄法生產(chǎn)的好;
2)生產(chǎn)難熔金屬材料和制品,一般要依靠粉末冶金法;
從制造機(jī)械零件方面來看,粉末冶金法制造的機(jī)械零件時(shí)一種少切削、無切削的新工藝,可以大量減少機(jī)加工量,節(jié)約金屬材料,提高勞動(dòng)生產(chǎn)率。
總之,粉末冶金法既是一種能生產(chǎn)具有特殊性能材料的技術(shù),又是一種制造廉價(jià)優(yōu)質(zhì)機(jī)械零件的工藝。
2粉末冶金的工藝原理
(1)生產(chǎn)粉末。粉末的生產(chǎn)過程包括粉末的制取、粉料的混合等步驟。為改善粉末的成型性和可塑性通常加入汽油、橡膠或石蠟等增塑劑。
(2)壓制成型。粉末在500~600MPa壓力下,壓成所需形狀。
(3)燒結(jié)。在保護(hù)氣氛的高溫爐或真空爐中進(jìn)行。燒結(jié)不同于金屬熔化,燒結(jié)時(shí)至少有一種元素仍處于固態(tài)。燒結(jié)過程中粉末顆粒間通過擴(kuò)散、再結(jié)晶、熔焊、化合、溶解等一系列的物理化學(xué)過程,成為具有一定孔隙度的冶金產(chǎn)品。
(4)后處理。一般情況下,燒結(jié)好的制件可直接使用。但對(duì)于某些尺寸要求精度高并且有高的硬度、耐磨性的制件還要進(jìn)行燒結(jié)后處理。后處理包括精壓、滾壓、擠壓、淬火、表面淬火、浸油、及熔滲等。
現(xiàn)代粉末冶金的主要工藝過程
生產(chǎn)粉末
制坯
燒結(jié)
1.壓制的原理
壓制就是在外力作用下,將模具或其它容器中的粉末緊密壓實(shí)成預(yù)定形狀和尺寸壓坯的工藝過程。鋼模冷壓成形過程如圖7.1.2所示。粉末裝入陰模,通過上下模沖對(duì)其施壓。在壓縮過程中,隨著粉末的移動(dòng)和變形,較大的空隙被填充,顆粒表面的氧化膜破碎,顆粒間接觸面積增大,使原子間產(chǎn)生吸引力且顆粒間的機(jī)械楔合作用增強(qiáng),從而形成具有一定密度和強(qiáng)度的壓坯。
2.等靜壓制
壓力直接作用在粉末體或彈性模套上,使粉末體在同一時(shí)間內(nèi)各個(gè)方向上均衡受壓而獲得密度分布均勻和強(qiáng)度較高的壓坯的過程。按其特性分為冷等靜壓制和熱等靜壓制兩大類。
?、爬涞褥o壓制
即在室溫下等靜壓制,液體為壓力傳遞媒介。將粉末體裝入彈性模具內(nèi),置于鋼體密封容器內(nèi),用高壓泵將液體壓入容器,利用液體均勻傳遞壓力的特性,使彈性模具內(nèi)的粉末體均勻受壓。因此,冷等靜壓制壓坯密度高,較均勻,力學(xué)性能較好,尺寸大且形狀復(fù)雜,已用于棒材、管材和大型制品的生產(chǎn)。
?、茻岬褥o壓制
把粉末壓坯或裝入特制容器內(nèi)的粉末體置入熱等靜壓機(jī)高壓容器中,施以高溫和高壓,使這些粉末體被壓制和燒結(jié)成致密的零件或材料的過程。在高溫下的等靜壓制,可以激活擴(kuò)散和蠕變現(xiàn)象的發(fā)生,促進(jìn)粉末的原子擴(kuò)散和再結(jié)晶及以極緩慢的速率進(jìn)行塑性變形,氣體為壓力傳遞媒介。粉末體在等靜壓高壓容器內(nèi)同一時(shí)間經(jīng)受高溫和高壓的聯(lián)合作用,強(qiáng)化了壓制與燒結(jié)過程,制品的壓制壓力和燒結(jié)溫度均低于冷等靜壓制,制品的致密度和強(qiáng)度高,且均勻一致,晶粒細(xì)小,力學(xué)性能高,消除了材料內(nèi)部顆粒間的缺陷和孔隙,形狀和尺寸不受限制。但熱等靜壓機(jī)價(jià)格高,投資大。熱等靜壓制已用于粉末高速鋼、難熔金屬、高溫合金和金屬陶瓷等制品的生產(chǎn)。
3.粉末軋制原理
將粉末通過漏斗喂入一對(duì)旋轉(zhuǎn)軋輥之間使其壓實(shí)成連續(xù)帶坯的方法。將金屬粉末通過一個(gè)特制的漏斗喂入轉(zhuǎn)動(dòng)的軋輥縫中,可軋出具有一定厚度、長(zhǎng)度連續(xù)、強(qiáng)度適宜的板帶坯料。這些坯體經(jīng)預(yù)燒結(jié)、燒結(jié),再軋制加工及熱處理等工序,就可制成具有一定孔隙度的、致密的粉末冶金板帶材。粉末軋制制品的密度比較高,制品的長(zhǎng)度原則上不受限制,軋制制品的厚度和寬度會(huì)受到軋輥的限制;成材率高為80%~90%,熔鑄軋制的僅為60%或更低。粉末軋制適用于生產(chǎn)多孔材料、摩擦材料、復(fù)合材料和硬質(zhì)合金等的板材及帶材。
4.粉漿澆注原理
是金屬粉末在不施加外力的情況下成形的,即將粉末加水或其它液體及懸浮劑調(diào)制成粉漿,再注入石膏模內(nèi),利用石膏模吸取水分使之干燥后成形。常用的懸浮劑有聚乙烯醇、甘油、藻骯酸鈉等,作用是防止成形顆粒聚集,改善潤(rùn)濕條件。為保證形成穩(wěn)定的膠態(tài)懸浮液,顆粒尺寸不大于5μm~10μm,粉末在懸浮液中的質(zhì)量含量為40%~70%。粉漿成形工藝參見本書6.2.2。
5.擠壓成形原理
將置于擠壓筒內(nèi)的粉末、壓坯或燒結(jié)體通過規(guī)定的??讐撼觥0凑諗D壓條件不同,分為冷擠壓和熱擠壓。冷擠壓是把金屬粉末與一定量的有機(jī)粘結(jié)劑混合在較低溫度下(40℃~200℃)擠壓成坯塊;粉末熱擠壓是指金屬粉末壓坯或粉末裝入包套內(nèi)加熱到較高溫度下壓擠,熱擠壓法能夠制取形狀復(fù)雜、性能優(yōu)良的制品和材料。擠壓成形設(shè)備簡(jiǎn)單,生產(chǎn)率高,可獲得長(zhǎng)度方向密度均勻的制品。
擠壓成形能擠壓出壁很薄直經(jīng)很小的微形小管,如厚度僅0.01mm,直徑1mm的粉末冶金制品;可擠壓形狀復(fù)雜、物理力學(xué)性能優(yōu)良的致密粉末材料,如燒結(jié)鋁合金及高溫合金。擠壓制品的橫向密度均勻,生產(chǎn)連續(xù)性高,因此,多用于截面較簡(jiǎn)單的條、棒和螺旋形條、棒(如麻花鉆等)。
6.松裝燒結(jié)成形原理
粉末未經(jīng)壓制而直接進(jìn)行燒結(jié),如將粉末裝入模具中振實(shí),再連同模具一起入爐燒結(jié)成形,用于多孔材料的生產(chǎn);或?qū)⒎勰┚鶆蛩裳b于芯板上,再連同芯板一起入爐燒結(jié)成形,再經(jīng)復(fù)壓或軋制達(dá)到所需密度,用于制動(dòng)摩擦片及雙金屬材料的生產(chǎn)。
將置于擠壓筒內(nèi)的粉末、壓坯或燒結(jié)體通過規(guī)定的模孔壓出。按照擠壓條件不同,分為冷擠壓和熱擠壓。冷擠壓是把金屬粉末與一定量的有機(jī)粘結(jié)劑混合在較低溫度下(40℃~200℃)擠壓成坯塊;粉末熱擠壓是指金屬粉末壓坯或粉末裝入包套內(nèi)加熱到較高溫度下壓擠,熱擠壓法能夠制取形狀復(fù)雜、性能優(yōu)良的制品和材料。擠壓成形設(shè)備簡(jiǎn)單,生產(chǎn)率高,可獲得長(zhǎng)度方向密度均勻的制品。
7.爆炸成形原理
借助于爆炸波的高能量使粉末固結(jié)的成形方法。爆炸成形的特點(diǎn)是爆炸時(shí)產(chǎn)生壓力很高,施于粉末體上的壓力速度極快。如炸藥爆炸后,在幾微秒時(shí)間內(nèi)產(chǎn)生的沖擊壓力可達(dá)106MPa(相當(dāng)于107個(gè)大氣壓),比壓力機(jī)上壓制粉末的單位壓力要高幾百倍至幾千倍。爆炸成形壓制壓坯的相對(duì)密度極高,強(qiáng)度極佳。如用炸藥爆炸壓制電解鐵粉,壓坯的密度接近純鐵體的理論密度值。
爆炸成形可加工普通壓制和燒結(jié)工藝難以成形的材料,如難熔金屬、高合金材料等,還可壓制普通壓力無法壓制的大型壓坯。
除上述方法外,還有注射成形及熱等靜壓制新技術(shù)等新的成形方法。
- 聯(lián)系我們
銷售經(jīng)理:王經(jīng)理
移動(dòng)電話:18939000078銷售熱線
電 話:0379-64122001
0379-64122002技術(shù)中心
電 話:0379-64122008
電子郵箱:techsupport@sbi.com.cn
地 址:中國(guó)洛陽(yáng)市西工區(qū)河南洛陽(yáng)工業(yè)園區(qū)緯四路
傳 真:0379-64122006
電子郵箱:sbi@sbi.com.cn
-